Ore properties
The main component of limestone is calcium carbonate (CaCO3), which can be directly crushed into crushed stone aggregate for the production of building materials, or it can be burned into quicklime through specific equipment. Quicklime can be used in large quantities for desulfurization in power plants, and quicklime will become hydrated lime after absorbing moisture or adding water. The main component of slaked lime is calcium hydroxide Ca(OH)2, which can be mixed with other materials to make limestone slurry, lime paste, etc. It is often used as a coating material and brick binder. At the same time, limestone is also an important raw material for many industrial production.
Processing process
Vibrating feeder + jaw crusher (stone crusher) + impact crusher + circular vibrating screen, jaw crusher and impact crusher are classic limestone crushing combinations, which are very good in the field of stone crushing in sand and stone plants The processing effect. The specific crushing method is to use a Raymond mill or a high-pressure mill to pulverize, classify, and separate the white stone containing more than 90% CaCO3 to obtain the finished product.
The first stage: coarse crushing
Large pieces of limestone are uniformly fed to the jaw crusher through the silo by the vibrating feeder for coarse crushing. After the coarsely crushed materials are screened by the vibrating screen, they are transported to the impact crusher by a belt conveyor.
The second stage: medium and fine crushing
After the materials to be processed transported to the impact crusher are crushed by the impact crusher, a circular vibrating screen is used to screen the crushed materials after the impact crusher. Larger particles are returned to the impact crusher and broken again. For finer products or shaping, the crushed materials are sent to the sand making machine for further crushing and shaping.
The third stage: milling
The crushed small pieces of limestone are sent to the silo by a hoist, and then sent to the grinding chamber of the ultra-fine mill in a uniform and quantitative manner by a vibrating feeder for grinding.
Introduction of Superfine Grinding Mill
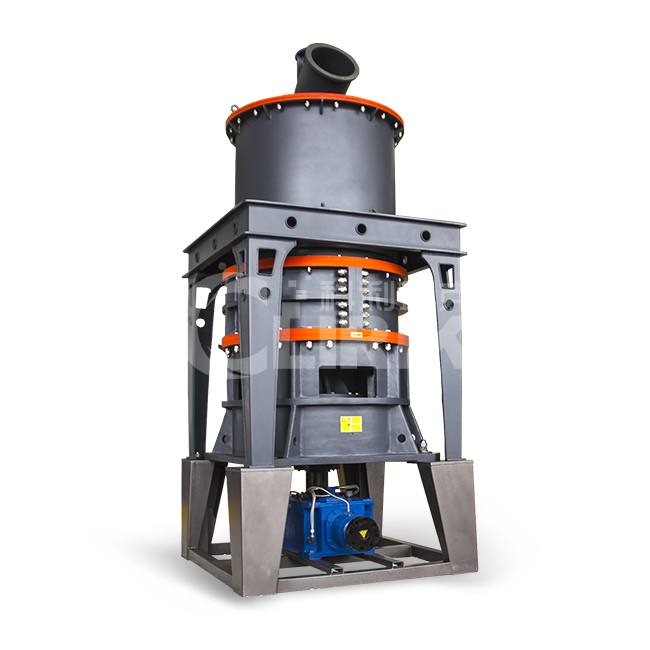
HGM ultrafine powder mill
The newly designed grinding roller grinding ring grinding curve improves the grinding efficiency. The production capacity is 40% higher than that of jet mills and stirring mills, and the energy consumption is only 30% of that of jet mills.
Equipped with multi-head cage type powder concentrator. The fineness of the product can be adjusted arbitrarily between 150-3000 mesh, and the one-time screening rate can reach d97≤5μm.
The lubrication device is installed outside the main shaft, which can realize external non-stop lubrication and continuous production for 24 hours.
HGM ultrafine grinding mill is equipped with a high-efficiency pulse dust collector, so there will be no dust pollution during the operation of the entire crushing system. Equipped with silencer and anechoic room to reduce noise.
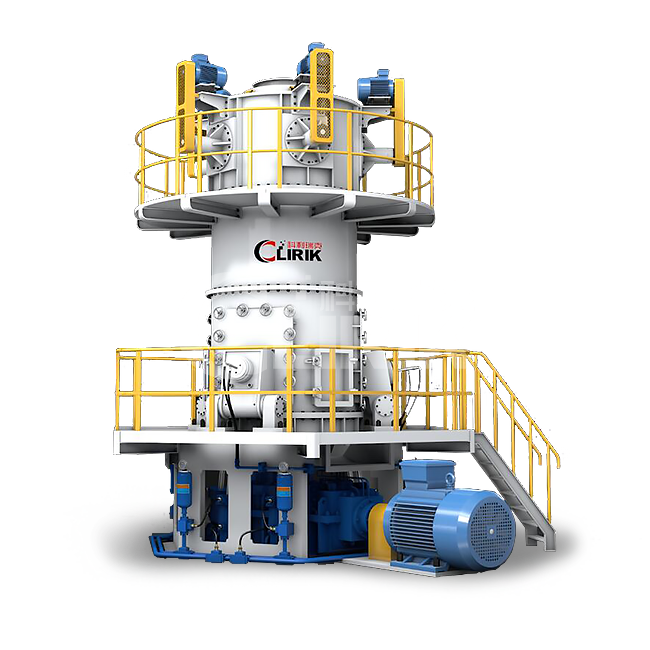
CLUM vertical roller mill
SBM specially designed a unique roller shell and liner grinding curve, which can greatly improve the working efficiency of the mill and improve the whiteness and cleanliness of the finished product.
Using a PLC control system and multi-head powder selection technology, it can precisely control the working parameters of the equipment such as grinding pressure and speed. Compared with ordinary mills, the energy consumption of this mill can be reduced by 30%-50%.
The contact point between the roller shell and the grinding disc liner adopts electronic limit technology and mechanical limit protection technology, which can avoid the destructive impact caused by machine vibration and ensure the stability of operation.
Through the reversible structure and hydraulic adjustment system, the operator can easily and quickly move the grinding roller out of the machine body, inspect and replace the roller shell and liner, and perform other maintenance operations to reduce downtime losses.